The V battery was commissioned in 2004 and is still in operation today, with continued production in three shifts. GIKIL’s Coke Plant t uses the technology of “renewable by-products”. The production process starts by defining the types of coking coal suitable for producing the specified coke quality required by the customer.
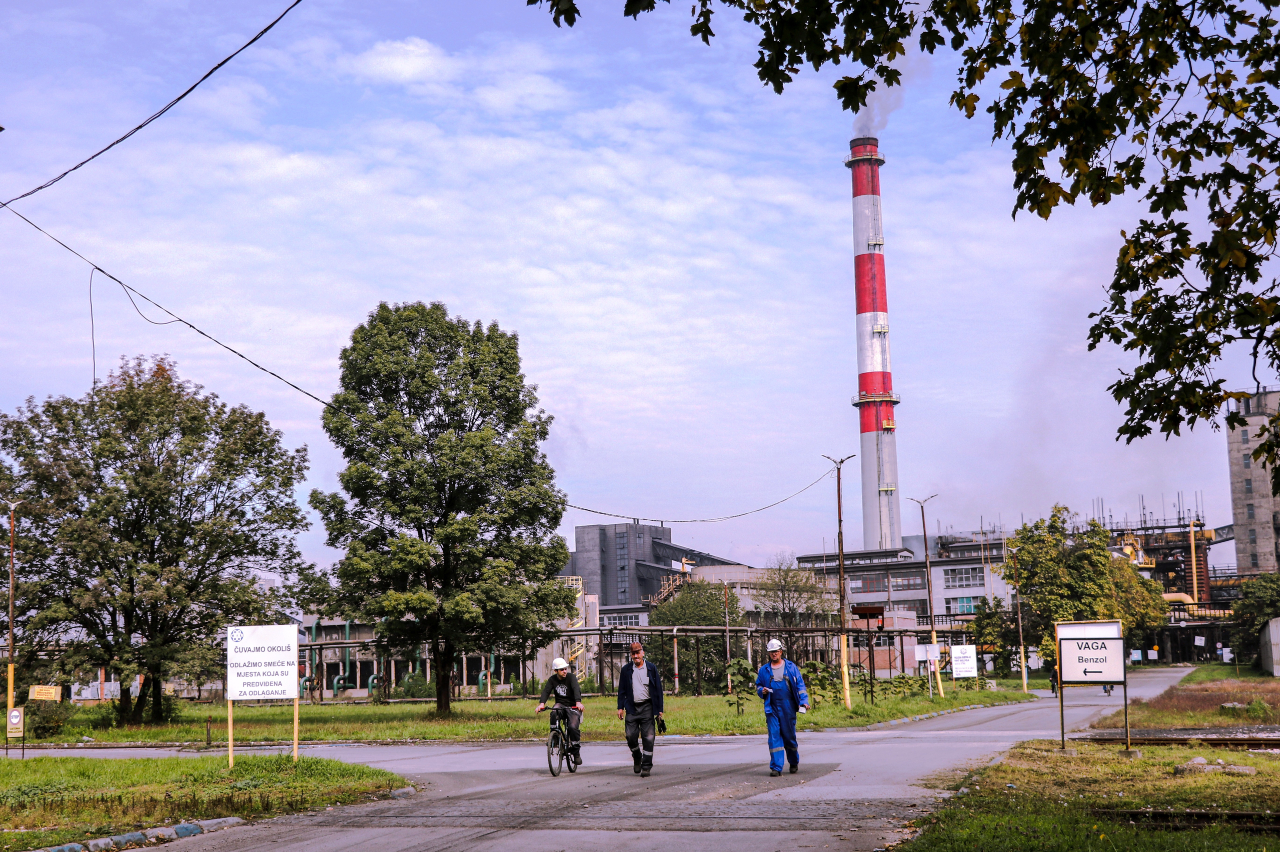
The V battery was commissioned in 2004 and is still in operation today, with continued production in three shifts. GIKIL’s Coke Plant t uses the technology of “renewable by-products”. The production process starts by defining the types of coking coal suitable for producing the specified coke quality required by the customer.
The quality and proportions of the various coals in the blend have the most important impact on the coke quality. There is some level of substitution, but the objective is to reduce raw material costs subject to coke specification constraints.
The coking coal is delivered by rail from the port of Ploče to the storage facilities in Lukavac. It is then transported by computer-controlled conveyor to the handling area where blends of several types of coking coal are made based on the required quality.
The blend is transported to the top of the coke battery. The ovens are heated with purified coke gas from the coking process.
Coal is loaded into the oven from the top using a loading vehicle and further heated to over 1000°C without oxygen for 16 to 19 hours for metallurgical coke and 24 hours for foundry coke.
The coking process eliminates volatile substances while combining fixed carbon with residual ash. Volatile substances produce crude coke gas. The crude coke gas is collected by transfer systems and purified into a by-product unit.
In the purification process, ammonia, benzene, sulphur, carbon dioxide and crude tar are segregated.
The rest of the purified coke gas is used to heat the coke ovens and as fuel where necessary in the plant. GIKIL uses gas for steam generation in its power plant.
The by-products plant can produce, at full battery production, 28,336 tons of crude tar per year, 8,586 tons of crude benzene per year and 6,000 tons of ammonium sulphate per year and 2,500 tons of naphthalene per year by purifying 299,460 million Nm3 of coke gas.
The purification process begins with the initial cooling of the gas when the crude tar is separated from the rest of the crude coke gas.
Crude coke gas is transported by electrostatic tar scrubbers to remove the remaining solid impurities.
The continuous movement of the crude coke gas is provided by gas extractors.