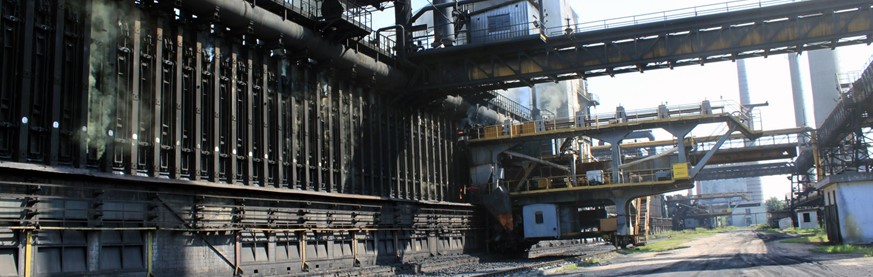
Efikasan proizvodni proces
GIKIL-ova fabrika koksara koristi tehnologiju „obnovljivih nus proizvoda“. Proizvodni proces počinje definiranjem koje vrste koksujućih ugljeva su pogodne da bi proizvele specificirani kvalitet koksa koji zahtijeva kupac. Kvaliteta i proporcije različitih ugljevlja u mješavini najviše utječu na kvalitet koksa. Ipak, postoji jedan određen nivo supstitucije. Cilj je smanjiti troškove sirovina koje su predmet ograničenja specifikacije koksa. Koksujući ugalj se isporučuje željeznicom iz luke Ploče u skladišne prostore u Lukavcu.
Zatim se transportuje pomoću kompjuterski-kontrolisanog sistema transportera u područje za manipulaciju gdje se od nekoliko vrsta koksujućeg uglja prave mješavine na osnovu potrebnog kvaliteta. Mješavina se transportuje na vrh koksne baterije. Svaka baterija se sastoji od 65 peći, koje su vatrostalne opeke zatvorene strukture. Peći se zagrijavaju pomoću pročišćenog koksnog gasa proizvedenog procesom koksovanja. Ugalj se puni u peći od vrha pomoću vozila za punjenje i dalje zagrijava na preko 1000°C bez kisika na 16 do 19 sati za metalurški koks i na 24 sata za livački koks. Proces koksovanja odvodi volatilne materije dok se fiksni ugljik i preostali pepeo spajaju. Volatilne materije stvaraju sirovi koksni gas (COG). Sirovi koksni gas se prikuplja kroz primopredajne sisteme i pročišćava u jedinici za nus-proizvode. Tokom procesa pročišćavanja, amonijak, benzol, sumpor, ugljična voda i sirovi katran se izdvajaju, a preostali pročišćeni koksni gas se koristi za zagrijavanje koksnih peći i kao gorivo gdje je potrebno u fabrici. GIKIL koristi gas za proizvodnju pare u svojoj fabrici za proizvodnju električne energije.
Process Flow: Dijagram za fabriku koksara
Koksara
Postrojenja za proizvodnju koksa se sastoje od dvije baterije (IV i V sa projektovanim kapacitetom od 0,7 M mt godišnje svaki). Svaka baterija ima 65 peći, koje su kontinuirano radile po rasporedu u tri smjene. Ukupni kapacitet stoga iznosi 1,4 M mt godišnje. Obje baterije su dizajnirane od strane ruske kompanije Giprokoks i funkcionisale na elektro-mehaničkom sistemu. Baterija V je isporučena neposredno prije početka rata i nije pokrenuta u to vrijeme. Baterija IV je dosegla 100% proizvodnog kapaciteta, ali je zaustavljena tokom rata i nije bila u funkciji posljednjih 21 godinu.
Obje baterije su bile dobro zaštićene i nisu pretrpjele nikakvu štetu tokom rata. Baterija V je puštena u rad 2004. godine, te će biti u mogućnosti da radi bez značajnih zastoja za kapitalne popravke tokom sljedećih 10 do 15 godina. Procjenjuje se treba oko 10 mjeseci da se obnovi i ponovno pokrene baterija IV. Duži popravci će eliminirati potrebu za kapitalne popravke u sljedećih 10 godina. Uprava vjeruje da s obzirom na potrebu finansiranja, baterija će biti operativna u roku od 10 mjeseci od povlačenja sredstava. Trenutna iskustva daju pretpostavku da će 90% proizvodnje obuhvaćati proizvodnju metalurškog koksa visokog stepena.
U punom kapacitetu dvije baterije su projektovane za proizvodnju 290 miliona kubičnih metara koksnog gasa na godišnjem nivou. Specificirane kvalitete sirovina i konačni proizvod se redovno prate u laboratoriji fabrike, dok se neki uzorci šalju dalje u nezavisne laboratorije.
Fabrika za proizvodnju nus-proizvoda
Kapacitet usluživanja fabrika za koksnu hemiju odgovara fabričkom kapacitetu koksovanja. Svrha jedinice za nus-proizvode je pročišćavanje sirovog koksnog gasa sa zadatkom uklanjanja vrlo vrijednih materijala poput sirovog katrana, benzola i amonijaka. Nakon tretmana, gas je spreman da se koristi za interno grijanje baterije i za proizvodnju energije u GIKIL-ovoj energani.
Fabrika za nus-proizvode može proizvesti, pri punoj proizvodnji baterije, 28.336 tona godišnje sirovog katrana, 8,586 tona godišnje sirovog benzola i 6.000 tona godišnje amonijum sulfata i 2.500 tona naftalina godišnje ispiranjem 299.460 miliona Nm3 koksnog gasa.
Proces čišćenja započinje primarnim hlađenjem gasa kada se sirovi katran odvaja od ostatka sirovog KOG. Sirovi KOG prolazi kroz elektrostatske taložnike katrana kako bi se uklonile sve preostale krute nečistoće. Kontinuirano kretanje KOG-a je osigurano ispušnicima plina. Sirovi KOG se konačno hladi prije ispiranja. Prva faza ispiranja je sa demineraliziranom vodom s ciljem uklanjanja amonijaka i djelomično sumpora. Ta amonijačna voda se obrađuje u postrojenju amonijum sulfata gdje se dobija finalni proizvod – amonijum sulfat.
Druga faza ispiranja je sa ispirnim uljem u cilju izvlačenja benzola iz sirovog KOG-a. Ispirno ulje sa apsorbiranim benzolom se obrađuje u postrojenju za destilaciju benzola gdje se odvaja sirovi benzol iz ispirnog ulja koje se vraća u proces ispiranja. Nakon posljednjeg procesa ispiranja gas je spreman za upotrebu i zove se čisti KOG.